Commercial renovations involve more than fresh finishes or updated layouts—they’re shaped by financial choices that ripple through every phase of the project. From office upgrades to retail reconfigurations, decisions made early on can contain costs or trigger expensive detours. Missteps often translate into mounting delays, strained budgets, and a renovation process that feels reactive instead of strategic.
Financial planning sets the foundation for better outcomes. Decisions around infrastructure, service coordination, and material sequencing impact more than just initial costs—they shape long-term efficiency and adaptability. When teams make clear, informed choices early on, they’re better prepared to handle challenges and keep the project moving smoothly from demolition to delivery.
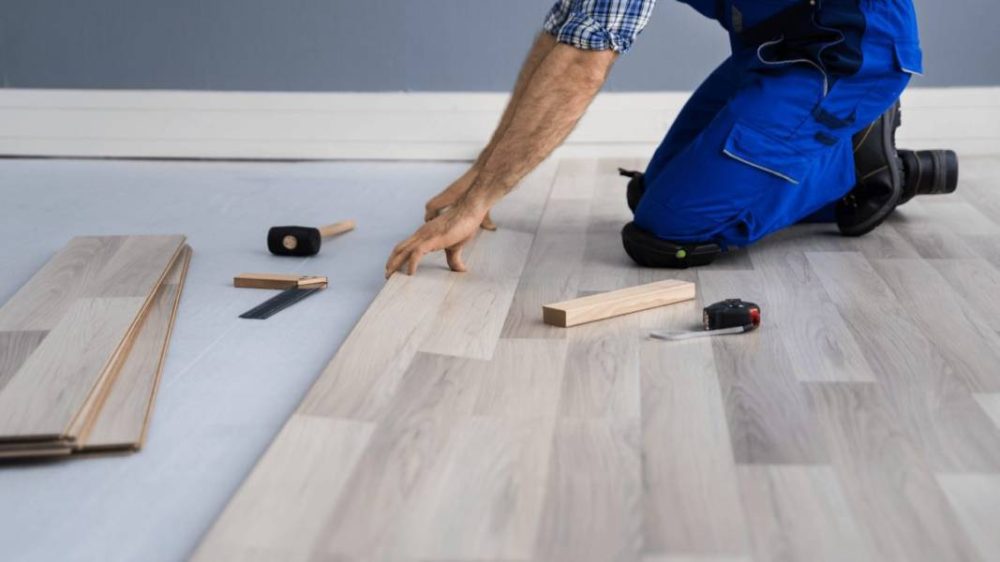
Choosing Scalable Power Infrastructure From the Start
Early decisions about electrical planning significantly shape the trajectory of commercial renovations. An overhead busway system stands out as a practical choice, providing flexibility for future adjustments in power requirements. It allows easy repositioning of access points without costly modifications to walls or slabs, helping maintain budget integrity.
Such a strategy not only accommodates changing business needs but also minimizes dependence on skilled electricians for adjustments. This feature proves advantageous in mixed-use or light industrial spaces, where power demands can alter over time. Considering the benefits of an overhead busway can streamline renovation processes while enhancing adaptability for the future.
Overcommitting to Permanent Fixtures Too Early
Installing permanent fixtures too soon can hinder the flow of a renovation project. Features like built-in casework or custom cabinetry might conflict with the final design layout, leading to complications that require expensive removals and a frustrating reinstallation process. This early commitment can turn into time-consuming setbacks, disrupting workflow and inflating costs unexpectedly.
Designing spaces effectively necessitates a thoughtful approach that prioritizes essential systems like plumbing and HVAC before adding those permanent touches. Sequencing installations based on finalized layouts helps minimize modification expenses later on. Taking time to establish foundational elements prepares the way for a smoother, cost-effective renovation.
Selecting Systems Without Lifecycle Flexibility
Opting for the lowest-cost systems might seem prudent at first, but it often results in hidden expenses over time. An HVAC unit with no room for future load increases may require full replacement within a few years—an outcome that severely disrupts operations and strains the budget. Flooring that appears durable at installation can quickly show wear in high-traffic areas, leading to ongoing maintenance that offsets any initial savings.
Electrical systems with limited capacity may not support equipment upgrades, triggering expensive rewiring and project downtime. Evaluating long-term functionality, not just purchase price, leads to smarter infrastructure choices. Selecting systems with room to adapt supports growth, reduces reactive spending, and maintains workflow continuity as needs change.
Misjudging Demolition vs. Integration Opportunities
Balancing demolition with reuse requires more than a visual assessment—it calls for a strategic understanding of structure, systems, and future use. Removing elements like structural walls or legacy mechanical shafts may appear straightforward, but these choices can trigger a cascade of unexpected costs, from added support requirements to code-mandated upgrades. In some cases, demolition may even expose previously hidden issues, such as outdated wiring or compromised plumbing.
Preserving functional components—like ductwork, framing, or conduit paths—can save significant resources if they meet current standards. Conducting a detailed pre-demolition evaluation with engineers and contractors helps identify what can be integrated safely and effectively. This approach protects both the schedule and budget while reducing waste and keeping renovation momentum intact.
Delaying Core Services Coordination Until Post-Design
Waiting to involve engineering and trade professionals until after architectural plans are finalized often leads to costly surprises. Structural adjustments required to reroute late-stage MEP (Mechanical, Electrical, Plumbing) systems can drive up expenses, introduce compliance challenges, and disrupt project flow.
These setbacks frequently delay labor schedules and inflate renovation costs. Engaging MEP experts early aligns core systems with the design vision, reducing the risk of rework. Strategic coordination supports smoother transitions between phases and helps maintain momentum across the entire project.
Smart cost management begins with early, informed decisions. Flexible power infrastructure like overhead busways reduces the need for disruptive changes later. Holding off on permanent fixtures prevents costly revisions when layouts change. Choosing scalable systems over short-term savings helps avoid premature replacements and frequent maintenance. Demolition should follow careful evaluation—retaining viable structures can cut down on labor and materials. Early collaboration with MEP professionals streamlines coordination and reduces rework. Each of these actions supports a renovation process that’s efficient, adaptable, and financially sound. Thoughtful sequencing and future-ready planning turn complex projects into opportunities for long-term value and operational ease.

HedgeThink.com is the fund industry’s leading news, research and analysis source for individual and institutional accredited investors and professionals